One of the most important stages in the lithium battery recycling line is metal separation, which is also the ultimate goal of our entire production line. If the separation efficiency is too low, it will waste human and financial resources. Therefore, our production line is equipped with a highly refined metal separation section to ensure the maximization of lithium battery recovery efficiency.
Efficient Metal Extraction from Recycled Lithium Batteries
During the crushing stage of the lithium battery recycling line, lithium batteries are crushed into particles. Since there are still some black mass that have not been removed, the lightweight materials, including positive and negative electrode powders as well as aluminum and copper foils, undergo further processing. The material is then fed into a drum sieve for powder separation. In fact, the most valuable material recovered here is the black substance, which contains rare metals. Next, let’s explore how to extract various metals using our equipment!
Advanced Techniques for Copper and Aluminum Separation
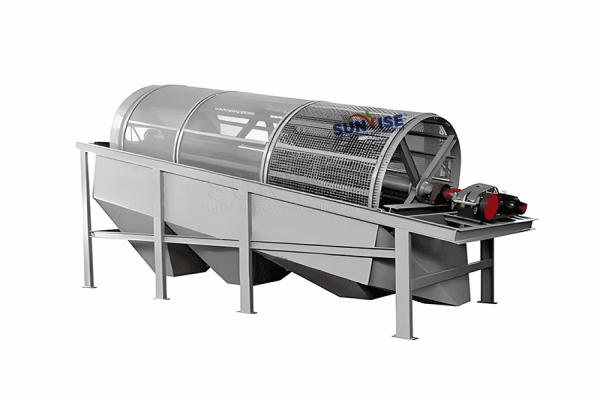
The drum sieve features a mesh structure and is fully enclosed. The sieve is made of 100-mesh stainless steel, allowing the black powder to be separated from the positive and negative electrode powders. The remaining tailings mostly consist of copper foils and aluminum foils, along with some casing and plastic separators. These tailings can go through additional crushing for further processing, achieving a black powder recovery rate of 97-98%. The remaining separators are removed once again, leaving copper and aluminum powder that can reach a particle size of 4mm.
The negative pressure collector (similar to a pulse dust collection principle) then feeds the remaining copper and aluminum into a grinder for finer grinding. This material is sent to a negative pressure collector and the vibrating screen for separating the remaining copper, aluminum, and black powder. The resulting powder can be sieved for purity based on customer requirements; if sieved, finer copper and aluminum can be separated.
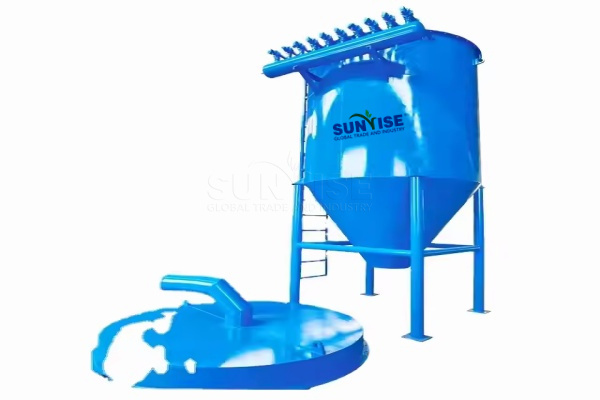
Utilizing Specific Gravity for Metal Purity in Recycling
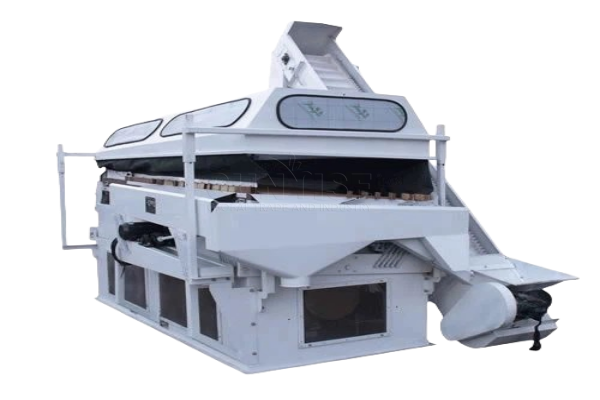
Specific Gravity Separation Machine: The copper-aluminum mixture can be separated using a specific gravity separation machine due to the difference in their densities. The front end produces heavier copper particles, while the back end yields lighter aluminum particles. The purity of copper can reach 92-94%, and aluminum purity can reach 80-85%. However, the material still contains some harder plastics, casings, and rubber from caps, leading to slightly higher aluminum impurities.
The large number of battery applications is an indisputable fact, the battery recycling and reuse to form a closed loop is the inevitable conditions for sustainable development. How to improve the recycling efficiency of the equipment and thus increase the customer’s income has always been our ultimate goal. SUNRISE will provide you with the most satisfactory machines!
Contact Us