Every year, over 1.5 billion scrap tires burden our planet as industrial “black pollution” – with the US discarding 300 million units and EU recycling 4 million metric tons.
However, this growing environmental crisis hides a golden business opportunity: modern tire recycling production lines now convert discarded rubber into high-value commodities like rubber powder, steel wires, and pyrolysis oil. As global demand for sustainable manufacturing soars, innovative factories are leveraging cutting-edge tire recycling equipment to turn ecological challenges into profitable ventures.
Today we’ll explore how automated tire recycling lines work, their ROI potential, and why they’re becoming must-have systems for forward-thinking waste management enterprises.
What Raw Materials are Suitable for Waste Tire Recycling Lines?
The waste tire recycling line can efficiently process various types of waste tires (rubber materials). Then turning them into valuable or reusable products. Below are some suitable raw materials that can be processed through waste tire recycling line.
What is the Waste Tyre Shredding Recycling Line?
Our waste tire recycling line includes a comprehensive array of specialized machines. This modular setup ensures that each stage of the recycling process is efficient, environmentally friendly, and produces high-quality output materials suitable for a range of applications.
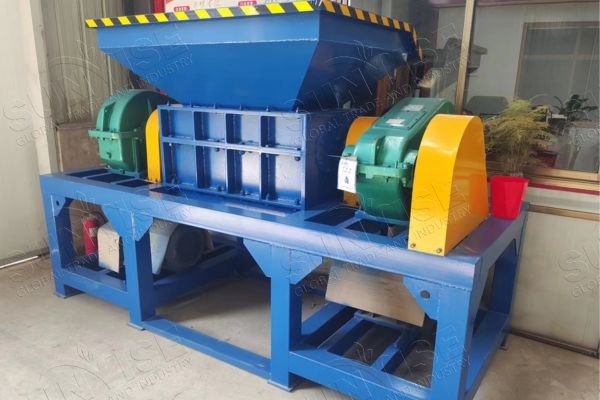
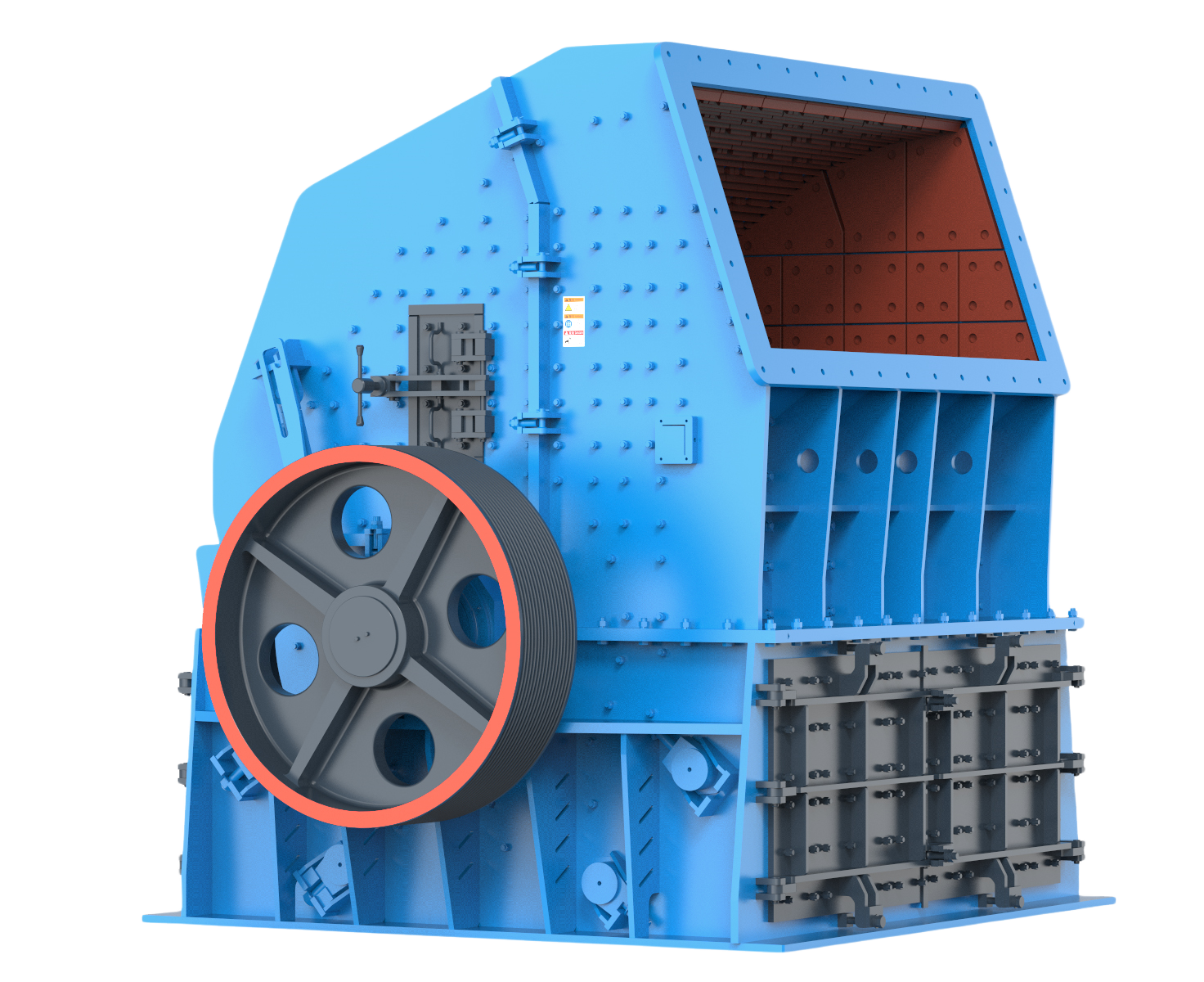
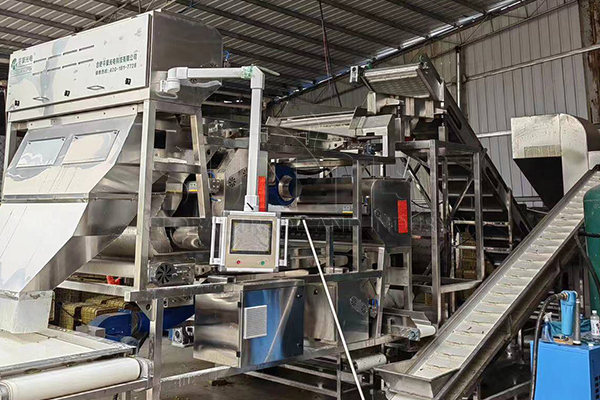
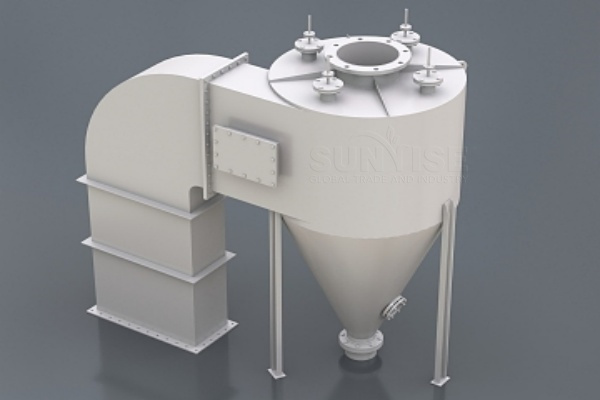
What Is The Process of Waste Tyre Pyrolysis Recycling Line?
The YSX waste tire pyrolysis recycling system represents an innovative industrial solution that leverages pyrolysis technology to transform end-of-life tires into commercially viable resources. This advanced recycling infrastructure not only provides an effective approach to managing waste tire accumulation but also enables the production of valuable by-products with significant economic potential.
Material Input
Waste tires or processed rubber powder are systematically fed into the pyrolysis reactor, serving as the primary feedstock for the conversion process.
Thermal Processing
The reactor is heated using various fuel sources, including tyre pyrolysis fuel oil, liquefied petroleum gas (LPG), natural gas, coal, or biomass. This heating phase initiates the pyrolysis reaction, prompting the chemical decomposition of tire materials at elevated temperatures.
By-Product Separation
As the temperature inside the reactor increases, gaseous hydrocarbons are released from the pyrolyzing tires. These vaporous components undergo a condensation process to form pyrolysis oil—a valuable output—while non-condensable gases undergo desulfurization and dust removal treatments. These treated gases can either be recycled to supply heat for the reactor or safely discharged into the atmosphere.
Reactor Cooling and Residue Extraction
Once the pyrolysis cycle is completed, the reactor is gradually cooled. Following this cooling phase, the solid residue—primarily composed of carbon black—is removed for further processing or utilization.
Emission Control
A dedicated exhaust gas purification system is employed to treat any remaining gaseous emissions, ensuring that all discharges meet strict environmental regulations and standards for air quality.
This integrated approach combines efficient material conversion with environmental responsibility, establishing the YSX tires pyrolysis recycling line as a sustainable solution for waste tire management and resource recovery.
Advantages of YSX Waste Tire Recycling Line
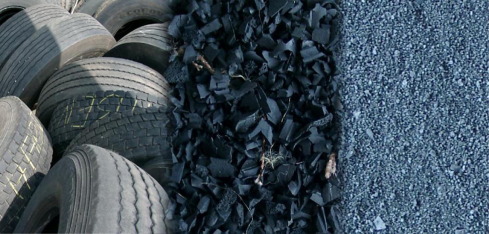
Want to know more about tyre recycling? Our team is here to help! We are available 24/7 to provide tyre recycling machines and solutions. Contact us anytime for professional support. We’re just a message away!
Contact Us