Receiving inquiries from clients interested in establishing a waste tyre recycling plant in Romania, like the one seeking a 10 – ton – per – hour capacity facility, is a common occurrence in our line of work. This article aims to comprehensively guide you through the process of building such a plant, covering everything from equipment to installation and more.
The Basics of a Romanian Waste Tyre Recycling Plant
Romania, with its growing automotive industry and increasing number of vehicles, generates a substantial amount of waste tyres. Building a recycling plant here not only helps in proper waste management but also contributes to the circular economy, creating economic opportunities and reducing the environmental footprint. So what are the key equipment for a 10 – ton – per – hour recycling plant?
The pyrolysis reactor is a crucial component for a recycling plant aiming for thermal decomposition of tyres.
For a 10 – ton – per – hour capacity, you need a high – efficiency pyrolysis reactor. These pyrolysis furnaces operate at high temperatures (usually around 400 – 600°C) in an oxygen – free environment.
They break down the rubber polymers in tyres into valuable by – products such as pyrolysis oil, carbon black, and combustible gas. A well – designed pyrolysis reactor should have excellent heat insulation to minimize energy loss and a reliable heating system to maintain a stable temperature.
Before the tyres enter the pyrolysis reactor, they need to be pre – processed.
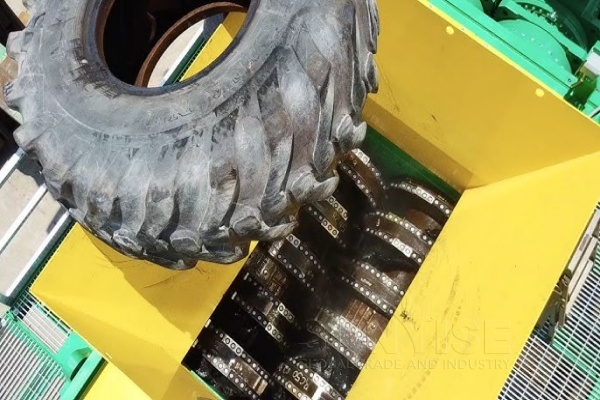
further crushes the primary crushed materials into 0.5-1 mm rubber fine powder, with its own air cooling system to prevent overheating and bonding, and an hourly output of 0.5-0.8 tons.
Shredders and crushers are used for this purpose. A large – capacity shredder can initially break down whole tyres into smaller pieces. This equipment should be robust enough to handle the tough rubber and steel components in tyres.
After shredding, crushers further reduce the size of the tyre pieces, making them more suitable for the pyrolysis process.
Once the tyres are processed, separation equipment is needed to isolate different materials.
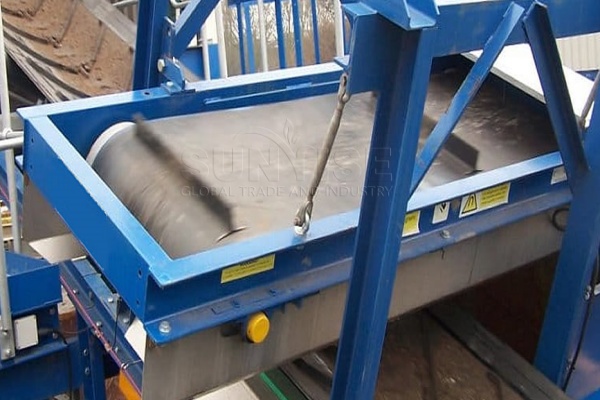
Placed on the crushed material conveyor belt, it recovers steel wire through strong magnetic adsorption, with a separation efficiency of more than 90%, and the purity of the recovered steel wire can exceed 85%.
Magnetic separators are used to extract the steel wires from the shredded and pyrolyzed tyre materials. Gravity separators or air – classifying separators can be employed to separate carbon black from other lighter materials. These separation processes ensure the purity of the recycled products.
For the pyrolysis process, a condensation system is essential to cool and liquefy the pyrolysis gas into pyrolysis oil.
This system consists of heat exchangers and condensers. Additionally, a gas treatment system is required to purify the combustible gas generated during pyrolysis. This treatment removes impurities such as sulfur and particulate matter, making the gas suitable for reuse as a fuel source within the plant or for other industrial applications.
Installation and Setup of a Romanian Waste Tyre Recycling Plant
Cost – Related Considerations
Compliance and Permits
Building a waste tyre recycling plant in Romania with a 10 – ton – per – hour capacity is a complex but rewarding endeavor. By understanding the key equipment requirements, installation processes, cost factors, and regulatory compliance, you can make informed decisions.
Whether you’re an entrepreneur looking to enter the recycling market or an existing business aiming to expand, careful planning and choosing the right supplier can help you build a successful and sustainable waste tyre recycling plant. If you have further questions or need detailed offers for your specific project, don’t hesitate to reach out to us.
Neem contact met ons op