More and more tyre recyclers are processing waste tyres into saleable materials and selling them. There are already professional waste tyre recycling lines on the market. Waste tyre recycling systems vary in design depending on capacity. This affects area occupancy, cost, labour, etc. Before purchasing a tire recycling line, we’d love to help you confirm your output. How about a processing capacity of 200 kg/h? On 7 October 2023, a customer from Singapore inquired us.
Here are the details of our communication on this case.
YUSHUNXIN: If you want to process 200kg of waste tires per hour, we can recommend you to choose our waste tire refining production line. It is an option for operating a small tire recycling production line.
There are two reasons: First, small waste tire refining production lines usually have a lower initial investment cost, while being able to recover the oil in the tires at a higher oil yield. It can meet production needs without causing excess equipment or waste of resources.
On the other hand, small equipment is usually designed to be more compact and simple, more flexible to operate, and usually has lower maintenance costs, which is suitable for limited space or start-up companies.
How To Design 200kg/h Tire Pyrolysis Production Line
It usually consists of a tire shredding machine, a pyrolysis reactor, a surface condenser for cooling and condensing the pyrolysis gases to obtain liquid products (such as pyrolysis oil), a gas purification and collection system, and a residue handling system for the solid residue (such as carbon black) left after pyrolysis. Contact us anytime, we’ll customize the pyrolysis solution for you.
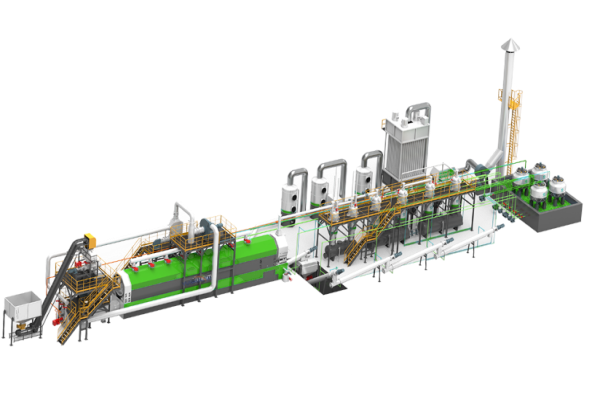
What Is The Design Of A 200kg/h Tire Pyrolysis Production Line
It usually consists of a tire shredding machine, a pyrolysis reactor, a surface condenser for cooling and condensing the pyrolysis gases to obtain liquid products (such as pyrolysis oil), a gas purification and collection system, and a residue handling system for the solid residue (such as carbon black) left after pyrolysis. Contact us anytime, we’ll customize the pyrolysis solution for you.
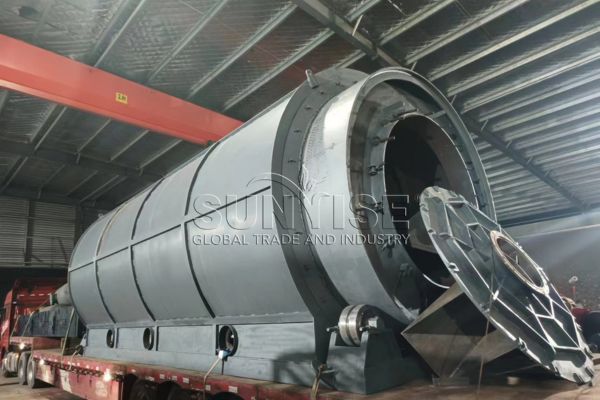
The Area Requirement of 200kg/h Tire Pyrolysis Production Line System
The Area Requirement of 200kg/h Tire Pyrolysis Production Line System
After knowing about the design, the customer in Singapore noticed the space requirements of the tire pyrolysis recycling line. He wanted to know if the workshop could accommodate a 200kg/h tire pyrolysis production line?
Generally speaking, a 200kg/h tire pyrolysis production line includes equipment, operating space, material storage and transportation channels, etc., and usually requires a workshop area of more than 500m2. Here is a detailed layout plan:
How Much Does A 200kg/h Tire Pyrolysis Production Line Cost
Generally, the cost of a 200 kg/h tire pyrolysis recycling production line can vary depending on various factors such as the quality of components, additional features, and brand.
However, you can expect to invest around $14,000 to $21,000. The exact cost would be determined after considering the specific requirements of the production line, such as the type of reactor, heating system, and cooling system used.
It’s important to note that these are just rough estimates and the actual cost would need to be calculated based on a detailed assessment of the equipment, installation, and any other associated costs such as transportation, installation labor, and after – sales service.
How Much Does A 200kg/h Tire Pyrolysis Production Line Cost
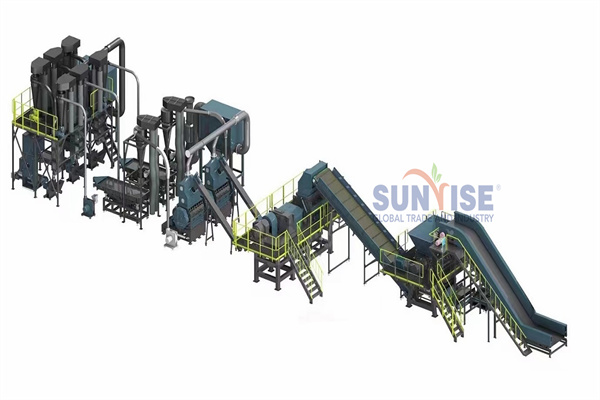
Generally, the cost of a 200 kg/h tire pyrolysis production line can vary depending on various factors such as the quality of components, additional features, and brand. However, you can expect to invest around $14,000 to $21,000. The exact cost would be determined after considering the specific requirements of the production line, such as the type of reactor, heating system, and cooling system used.
It’s important to note that these are just rough estimates and the actual cost would need to be calculated based on a detailed assessment of the equipment, installation, and any other associated costs such as transportation, installation labor, and after – sales service.
However, you can also tell us what you want to recycle from the tires? Pyrolysis oil or carbon black? You can determine the solution in this way.
If your objective is to obtain pyrolysis oil from a tire pyrolysis facility operating at 200 kg/h
Equipment Name | Extractable Product | Unit Price (Approximate) |
---|---|---|
Tire Shredding Machine | Prepares shredded tires for pyrolysis | $2,000 – $20,000 |
Pyrolysis Reactor | Initiates the pyrolysis process to produce pyrolysis gas | $40,000 – $200,000 |
Condenser | Condenses pyrolysis gas into liquid oil | $5,000 – $20,000 |
Oil – Gas Separator | Separates the condensed oil from uncondensed gas | $10,000 – $30,000 |
Oil Storage Tank | Stores the extracted pyrolysis oil | $3,000 – $8,000 |
**Total** | – | $145,000 |
If you want to recover carbon black from a 200 kg/h tire pyrolysis line
Equipment Name | Extractable Product | Unit Price (Approximate) |
---|---|---|
Tire Shredding Machine | Prepares shredded tires for pyrolysis | $2,000 – $20,000 |
Pyrolysis Reactor | Initiates the pyrolysis process to produce carbon black and other by-products | $40,000 – $200,000 |
Carbon Black Separator | Separates carbon black from other solid residues | $10,000 – $20,000 |
Carbon Black Storage Tank | Stores the extracted carbon black | $2,000 – $5,000 |
**Total** | – | $128,000 |
If your objective is to obtain pyrolysis oil from a tire pyrolysis facility operating at 200 kg/hIf your objective is to obtain pyrolysis oil from a tire pyrolysis facility operating at 200 kg/h
Equipment Name | Extractable Product | Unit Price (Approximate) |
---|---|---|
Tire Shredding Machine | Prepares shredded tires for pyrolysis | $2,000 – $20,000 |
Pyrolysis Reactor | Initiates the pyrolysis process to produce pyrolysis gas | $40,000 – $200,000 |
Condenser | Condenses pyrolysis gas into liquid oil | $5,000 – $20,000 |
Oil – Gas Separator | Separates the condensed oil from uncondensed gas | $10,000 – $30,000 |
Oil Storage Tank | Stores the extracted pyrolysis oil | $3,000 – $8,000 |
**Total** | – | $145,000 |
If you want to recover carbon black from a 200 kg/h tire pyrolysis lineIf you want to recover carbon black from a 200 kg/h tire pyrolysis line
Equipment Name | Extractable Product | Unit Price (Approximate) |
---|---|---|
Tire Shredding Machine | Prepares shredded tires for pyrolysis | $2,000 – $20,000 |
Pyrolysis Reactor | Initiates the pyrolysis process to produce carbon black and other by-products | $40,000 – $200,000 |
Carbon Black Separator | Separates carbon black from other solid residues | $10,000 – $20,000 |
Carbon Black Storage Tank | Stores the extracted carbon black | $2,000 – $5,000 |
**Total** | – | $128,000 |
The above is the specific content of our communication with the Singapore customer. In addition to the proposal of waste tire pyrolysis production line, we can also provide you with business plans for circuit board recycling, solar panel recycling and lithium battery recycling line. If you need it, please contact us at any time.
Contact Us