As the new energy electric vehicle (NEV) market continues to expand exponentially, the issue of vehicle recycling has emerged as a crucial aspect for the sustainable development of the industry. By 2025, we anticipate that recycling will not only be a necessity for environmental protection but also a potential source of valuable resources and economic opportunities. With the increasing number of end-of-life NEVs, proper recycling methods and infrastructure will be essential to handle the growing volume of discarded vehicles.
You can recycle which parts of new energy vehicles?
Recyclable items on new energy electric vehicle (NEV) surfaces
The window glass of NEVs can be shredded and recycled. This process involves breaking the glass into small pieces, which can then be melted and reformed into new glass products, reducing the need for virgin raw materials.
Additionally, the car body plastics, which are widely used in modern vehicle manufacturing for their lightweight and durable properties, can be crushed and processed to yield economic benefits. These recycled plastics can be used in various industries, such as the production of plastic pellets for manufacturing new plastic components or in the construction industry for non-structural applications.
Recyclable materials inside energy electric automobiles
Lithium batteries in new energy battery electric vehicles (BEV) are a significant source of precious metals. These batteries contain elements like lithium, cobalt, nickel, and manganese, which are in high demand for the production of new batteries. Through advanced recycling techniques, these precious metals can be recovered and reused, reducing the reliance on mining and the associated environmental impacts.
Lithium batteries in new energy battery electric vehicles (BEV) are a significant source of precious metals. These batteries contain elements like lithium, cobalt, nickel, and manganese, which are in high demand for the production of new batteries. Through advanced recycling techniques, these precious metals can be recovered and reused, reducing the reliance on mining and the associated environmental impacts.
Which machines can recycle valuable materials in new energy EVs
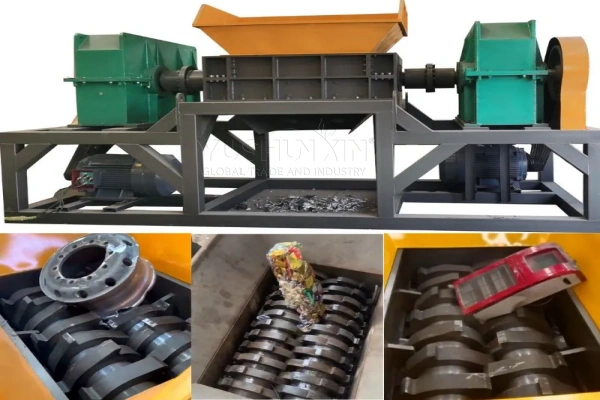
When it comes to recycling the car shells of new energy EVs, heavy-duty shredding machines are essential. These shredders can handle the large and sturdy metal structures. For example, hydraulic crushers with a powerful motor can exert high pressure to break down the car bodies into smaller pieces. They usually have a large crushing chamber and adjustable jaws to accommodate different sizes of car parts. The power of such crushers can range from 50 kW to 150 kW, enabling them to efficiently process the thick metal sheets of the car shells.
For the recycling of window glass, specialized crushers are required. These crushers are often equipped with toughened blades and a vibrating feeder system. The blades are made of high-quality alloy to withstand the hardness of the glass. The vibrating feeder ensures a continuous and even supply of glass pieces to the crushing area. Some advanced glass crushers can achieve a crushing size as small as 1 – 5 mm, which is crucial for further processing and separation of the glass components. The power consumption of these crushers is relatively lower compared to those for car bodies, typically around 10 kW to 30 kW.
Circuit boards in new energy EVs contain valuable metals and components. Crushers designed for circuit boards need to be more precise and gentle to avoid damaging the precious materials. They usually employ a combination of mechanical shearing and impact forces. The crushers have fine-toothed rollers and a controlled crushing mechanism to break the circuit boards into small fragments while preserving the integrity of the metals and semiconductors. The power of these crushers is generally in the range of 20 kW to 50 kW.
Vibrating screens with different mesh sizes are commonly employed. These screens can separate the crushed materials based on their particle size. For example, a vibrating screen with a mesh size of 2 – 10 mm can effectively sift out the aluminum particles from the non-metallic debris. The screening efficiency is crucial to ensure the purity of the recovered metal elements. Our screening machines are equipped with intelligent control systems to adjust the vibration frequency and amplitude, optimizing the separation process.
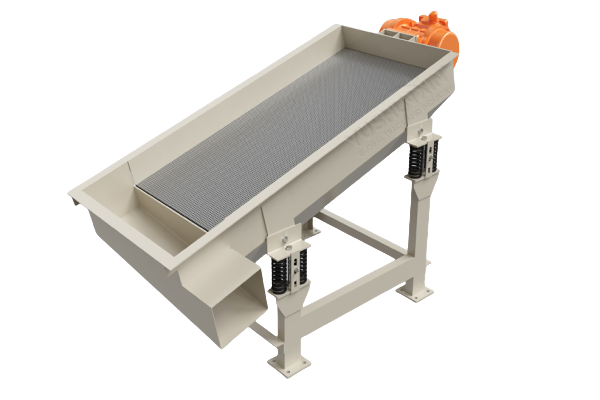
Magnetic vibrating screens are widely used for separating metal elements. These screens utilize the magnetic properties of metals to attract and separate them from the non-metallic materials. They consist of a vibrating deck with built-in magnets and a variable-frequency drive system. The magnetic field strength can be adjusted according to the type and size of the metal particles to be recovered. For example, for small metal fragments, a magnetic field strength of 2000 – 3000 Gauss is sufficient, while larger pieces may require a stronger field of 4000 – 5000 Gauss. The vibrating motion helps to move the materials along the screen surface, allowing the metal particles to be captured by the magnets and diverted to a separate collection chute. Additionally, our screen mesh size can be customized, typically ranging from 0.5 mm to 5 mm, to further refine the separation process and ensure the purity of the recovered metal elements.
In conclusion, the recycling of valuable materials in new energy EVs requires a combination of specialized recycling machines, each tailored to the specific characteristics of the materials being recycled. If you are an enterprise or individual interested in delving deeper into the field of new energy vehicle parts recycling, or if you have any questions regarding the selection of recycling equipment, contact us please. Our team is here to assist you.
How to ensure that the waste car recycling process is pollution-free
By implementing these pollution prevention measures, you can ensure that the waste car recycling process is environmentally friendly. We specialize in providing top-notch e-waste recycling solutions including dust removal. You can reach out to us via our contact form. We look forward to helping you enhance the environmental performance of your e-waste recycling business through our high-quality dust removal equipment.
How can recycling new energy vehicle parts bring you profits?
In 2025, the recycling of new energy electric vehicle parts offers great economic promise. Advanced recycling technologies help unlock the value of discarded vehicles.
We manufacture professional recycling equipment with CE and ISO certifications. Our offerings include lithium – battery recycling machines, solar panel recycling equipment, circuit – board recycling lines, and tire pyrolysis production line equipment.
If you’re interested in the new energy EV recycling business and unsure about equipment choices, contact us without hesitation.
Contact Us