YSX lithium battery recycling machine production line can be used to recycle cylindrical batteries, prismatic batteries, pouch battery negative plates, positive plates, etc., which can be directly put into the machine without any processing.
Lithium batteries are mainly composed of shell, positive electrode, negative electrode, electrolyte and diaphragm. The final products are graphite powder, aluminum particles, copper particles, plastic, steel shell, diaphragm plastic, etc.
From an environmental protection perspective, our production line is outfitted with top-notch air purification equipment. We’ve installed a water spray system and an activated carbon unit. The water spray system helps to trap and neutralize pollutants, while the activated carbon unit is highly effective at soaking up unpleasant odors. On top of that, there’s a pulse dust collection system in place. This system works like a charm, using short, powerful pulses of air to efficiently adsorb dust particles.
Raw Materials Suitable for Lithium Battery Recycling Machines
Raw materials for lithium battery recycling machines are diverse. Cellular li-ion batteries, soft pack, 18650, and aluminum shell lithium batteries are common. Their negative and positive plates, holding valuable metals, are also crucial. These materials are key for efficient recycling to recover resources. If you have lithium batteries of other types not listed here, or if you’re unsure whether your used batteries are compatible with our recycling equipment, don’t hesitate to reach out to YSX Eng. Dept. We’ll assess their suitability for our machines. Additionally, we provide customization services tailored to your unique requirements.
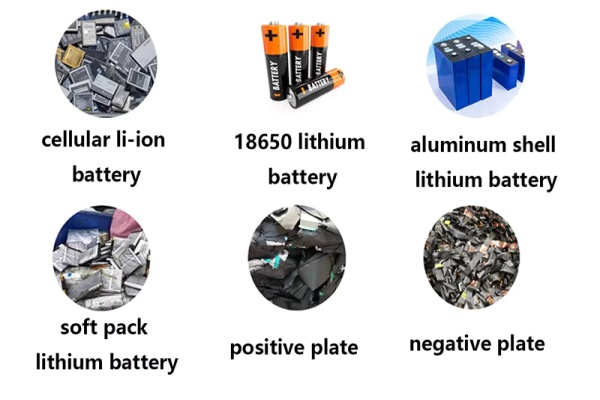
Discharging Lithium Batteries Before Recycling Lithium-ion Batteries
Because of the high reactivity of lithium, recycling requires extra precautions for safety–battery discharging. That is to say, before a battery goes for recycling, it needs to be fully discharged to minimize fire risk. For now, discharging goes through these several ways.
Salt Water Discharge Method of Lithium Batteries
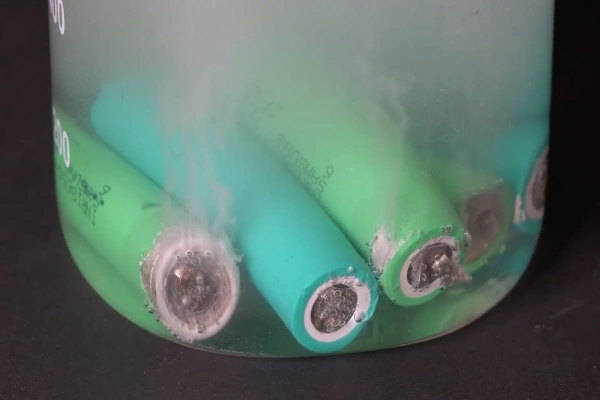
Advantages:
1. Simple and easy: The salt water discharge method is simple to operate and does not require complex equipment or professional technicians to perform.
2. Low cost: As we all know, salt water is a cheap and readily available material. Therefore, the implementation cost of this method is low.
Pay attention:
1. Slow speed: Salt water discharge may take a long time to fully discharge, about 1-2 days.
2. Evaporate the water cleanly: There will have safety hazards if you don’t pay attention on it. Wet batteries may leak, release gas or other dangerous situations.
3. Avoid mixing: Applicable battery types are soft pack, plastic hard shell battery and cylindrical battery. Batteries of other different types or states should not be discharged together to avoid danger.
Working Principle:
The charged lithium battery is fed into the gap between the needle roller and the groove roller through the feeder. Through rotation and extrusion, the steel needle attached to the needle roller pierces the inside of the battery, causing a short circuit between the positive and negative electrodes, thereby releasing energy and achieving the purpose of discharge. In addition, by adjusting the gap between the two rollers, the discharge requirements of different types of lithium-ion batteries can be met.
Attention:
It is mainly for 3C product batteries such as soft packs and plastic hard shells.
Needle Discharge Technique for Lithium Battery
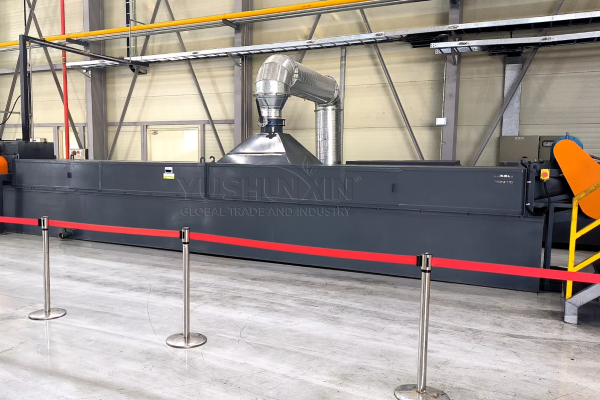
Employing Roll Cutting Discharge for Lithium Batteries
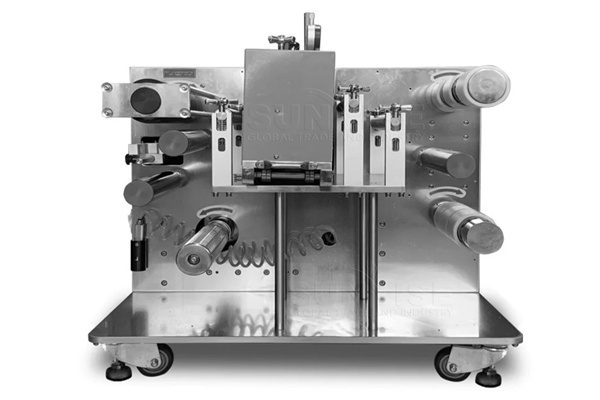
Working Principle:
Lithium-ion battery roll-cutting discharge equipment works simply. First, the rolling part rotates the battery. Then, a cutter slices open the battery case. Once opened, the positive and negative electrodes inside touch, causing a short – circuit. This short – circuit makes the battery discharge its electricity fast. The equipment also has safety checks, like sensors to monitor heat and smoke.
Attention:
The applicable battery is a cylindrical lithium-ion battery.
What is the Lithium Batteries Recycling Process?
Shredding the Batteries
Batteries are fed into a shredder to break them into smaller pieces. One shred is 10cm long and 4cm wide and the second crushing is 3-4cm long and 2cm wide.
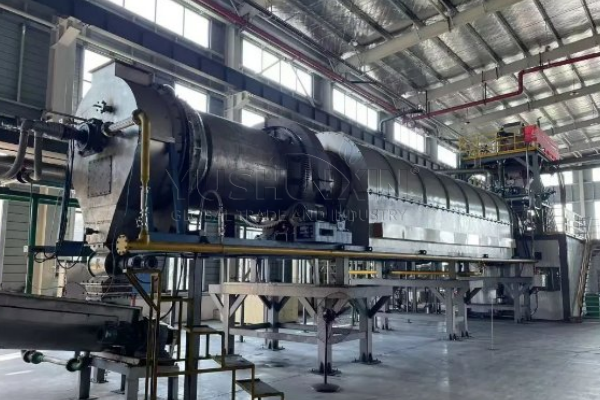
Pyrolysis of Batteries
Utilizing high temperature to make the internal components of the battery undergo pyrolysis reaction, it takes one and a half hours and can improve the purity of black powder by 4-5%.
High-temperature cracking technology not only better retains the valuable metal elements inside the battery, such as cobalt, nickel, lithium, etc., and improves the efficiency of battery recycling, but also greatly reduces the emission of hazardous substances that may be produced during the recycling process, and reduces the pollution of the environment.
Separation of Lithium Battery Recycled Materials
Advanced mechanical and physical separation techniques are used in lithium-battery recycling. Processes like Z-type separation, vibrating screening, drum screening, magnetic separator, gravity separating, three-stage and four-stage crushing, along with linear and disc screening, isolate various materials. Metals, plastics, and the black mass with lithium, cobalt, nickel, and manganese are effectively separated for resource recovery.
At this point, after crushing, several types of substances will be decomposed, in addition to liquid electrolyte and black substances, there are also used to make the battery positive and negative aluminum and copper foil, plastic diaphragm and so on. This is the end of a complete lithium battery recycling process.
Check out the video below to see YSX machines in action at our factory. We cordially invite you to visit and witness our top-notch recycling equipment first-hand. Experience the precision and efficiency that sets our machinery apart!
What Final Products You Can Get in Lithium Batteries Recycling?
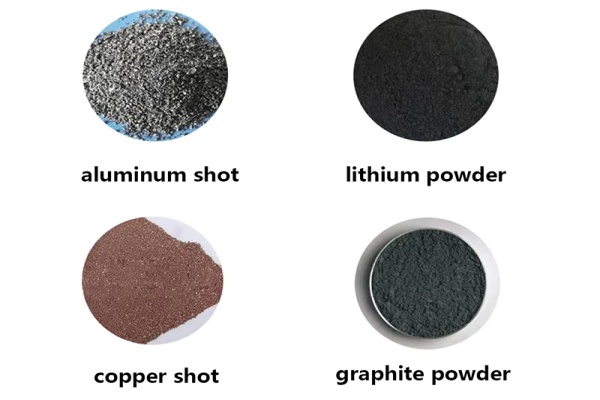
In lithium battery recycling, various valuable final products can be obtained. Aluminum shot is recycled from battery casings, useful in metalworking. Copper shot, retrieved from wiring, is highly conductive for electronics. Lithium powder, a key component, is vital for new battery production. Graphite powder, from electrodes, has applications in batteries and lubricants.
How to Design A lithium Battery Recycling Factory?
Below are some of the key aspects that need to be considered in the plant design. These specific design measures will help ensure the efficient, safe, and environmentally friendly operation of your waste lithium-ion battery recycling facility.
From the Perspective of Process Optimization
Reasonable functional area division can greatly improve work efficiency. It is recommended to divide the plant into five main areas: receiving area (100-300 ㎡), disassembly area (150-400 ㎡), classification area (100-300 ㎡), processing area (100-400 ㎡) and storage area (50-300 ㎡). Each area should have clear boundaries to reduce cross contamination and operational confusion.
A channel with a width of not less than 2 meters should be set to ensure smooth passage of forklifts and other transportation equipment, thereby reducing handling time.
From the Perspective of Safety Design
At least one fire extinguisher should be equipped for every 100 m2, and a fire sprinkler system should be installed in key areas. Regularly conduct safety drills once a quarter to ensure that workers are familiar with the operating procedures in emergency situations.
What are the Costs of a Lithium Battery Recycling Plant?
The cost to break the battery down lithium batteries is depend on the volume you want.
1. For a recycling factory with an hourly output of 300 – 500 kg
The price range is between $50,000 and $100,000. The equipment involved includes shredders, crushers, screening machines, and separation equipment, etc. The total floor area spans from 300 to 500 ㎡.
2. When it comes to a recycling factory having an hourly output of 500 – 800 kg
The price range is from $100,000 to $300,000. The total area lies between 500 and 600 ㎡.
3. In the case of a recycling factory with an hourly output of 800 – 1200 kg
The price range is from $300,000 to $450,000. It’s a large automatic recycling prodution line. The total floor area is from 600 to 900 ㎡.
How About Our Customer Feedback of Lithium Battery Recycling Machines?
I’m not sure how to dispose the large amount of waste lithium batteries I had, thanks for YUSHUNXIN giving me good advice and proposal. Building a circular supply chain will help me maintain business stability into the future. Thanks!
I process around 300 kilograms of used car batteries and other lithium batteries every day. Since I started using YSX’s battery recycling production line equipment, it’s been amazing. I can efficiently extract and reuse those crucial battery materials. Seriously, I’m super grateful. You guys have really helped me out a ton.
Contact Us