Did you know the global tire recycling market is projected to reach $7.15 billion by 2030? As you plan your scrap tire recycling plant, the first and most important information you need to know is the cost of waste tyre recycling plant. This comprehensive guide breaks down waste tire recycling plant costs with precision, analyzing key machinery investments and hidden operational expenses. Let’s start with key equipment parameters, specific costs, and price differences based on production capacity.
Costs of Essential Machinery for a Waste Tyre Recycling Facility
As the cornerstone of any tire recycling operation, industrial-grade tire shredders transform whole tires into 2-5cm rubber chips ready for downstream processing. A high-capacity shredder capable of processing 2 tons per hour typically costs between $150,000 and $300,000. For smaller operations of tyre recycling plant, a shredder with a capacity of 500 kg per hour might cost around $50,000 to $100,000.
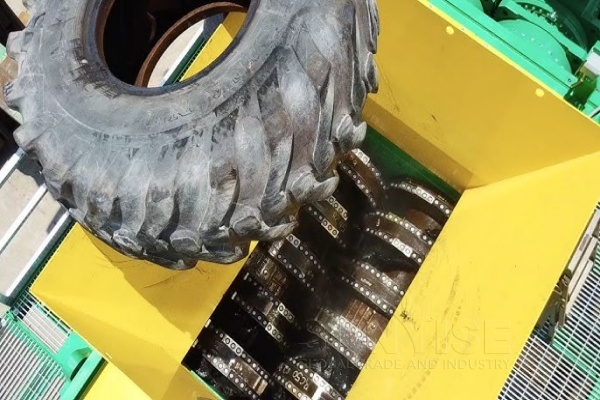
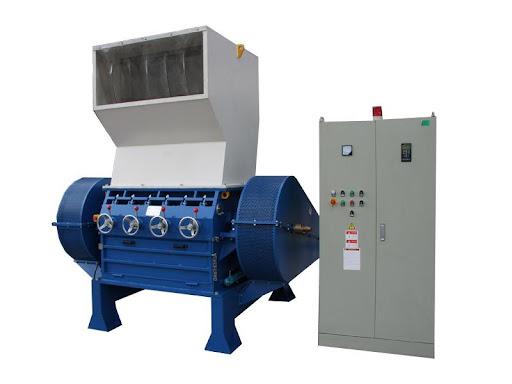
Steel Wire Separator
After shredding, the steel wire separator removes the steel wires from the rubber. A high-efficiency separator for processing 1 ton per hour is priced at approximately $80,000 to $150,000.
Rubber Granulator
This machine grinds shredded rubber into granules or powder. Prices for granulators range significantly based on capacity. For instance, a granulator with a capacity of 1 ton per hour might cost $200,000 to $350,000. Smaller units with a capacity of 300 kg per hour can cost around $70,000 to $150,000.
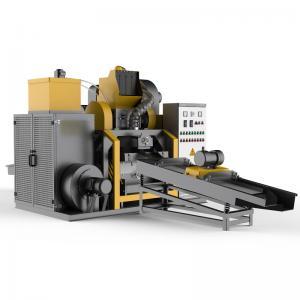
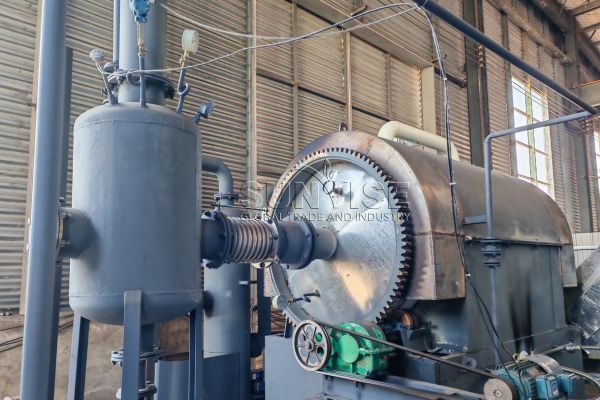
Pyrolysis Reactor
For further processing, pyrolysis reactors convert rubber granules into oil, gas, and other by-products. A reactor with a daily processing capacity of 10 tons may cost between $300,000 and $600,000. For medium-scale operations, a reactor with a capacity of 5 tons per day might cost around $200,000 to $400,000.
Shredding → Separating → Pyrolysis
Operating Costs of a Scrap Tire Recycling Plant
Permit Costs
Facility Costs
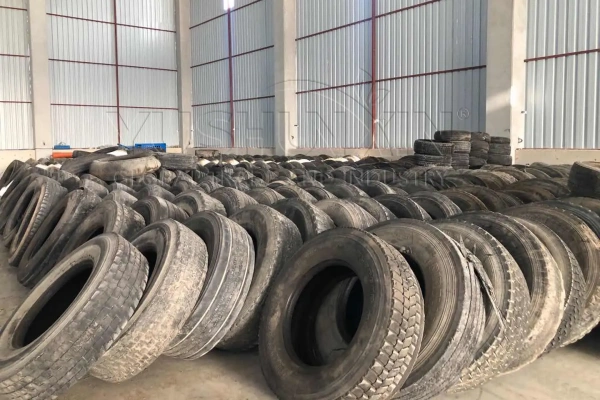
Energy Consumption and Costs
- 1
Electricity: A plant processing 10 tons per day may consume around 1,500 kWh of electricity daily, resulting in a monthly electricity cost of approximately $4,500 (assuming $0.10 per kWh). Smaller plants processing 2 tons per day might have monthly electricity costs around $900.
- 2
Fuel: For pyrolysis reactors, fuel costs vary. Using natural gas or diesel might add an additional $2,000 to $4,000 per month for a 10-ton per day plant.
Labor Costs
- 1
Technicians and Operators: Salaries for skilled technicians range from $40,000 to $60,000 annually. A 10-ton per day plant might require 5 to 8 technicians, resulting in annual labor costs of $200,000 to $480,000. Smaller plants might need 2 to 3 technicians, costing between $80,000 and $180,000 annually.
- 2
Administrative Staff: Including administrative staff costs, you may need to budget an additional $50,000 to $100,000 annually.
Maintenance and Consumables
- 1
Routine Maintenance: Budget around 5% to 10% of the total machinery cost annually for maintenance. For a plant with an initial machinery investment of $1,000,000, annual maintenance costs might be $50,000 to $100,000.
- 2
Consumables: Items like filters, lubricants, and other consumables can add another $10,000 to $20,000 annually.
Regional cost differences of tyre recycling plant
Two Tips for Managing Tire Scrap Recycling Costs
I. Optimize the Collection Process
That is to say efficient transportation planning. One of the significant costs in tire scrap recycling is transportation. Plan your collection routes. If you have multiple suppliers in a particular industrial area, arrange to collect from them all in one trip rather than making multiple short trips.
Moreover, partnerships facilitate centralized collection. Form partnerships with local tire dealerships, auto repair shops, and vehicle fleets. By agreeing to collect their waste tires regularly, you can ensure a steady supply and potentially reduce collection costs.
II. Tire Recycling Machine Selection and Maintenance
Right – Sized Equipment
When choosing tire recycling equipment such as shredders, make sure to select the right size for your operation. Buying equipment that’s too large for your current volume of tire scraps will lead to higher capital costs and potentially wasted energy. On the other hand, equipment that’s too small may not be able to handle the workload efficiently, leading to increased processing time and costs.
Consider the future growth of your business when selecting equipment. Look for machines that can be upgraded or expanded in capacity relatively easily. To solve this problem, we can offer you modular equipment that allows you to add components later as your needs increase. Contact us to know more.
Regular Maintenance
Implement a strict maintenance schedule for your recycling equipment. Regular maintenance can significantly extend the life of your machines and reduce the risk of costly breakdowns. For example, lubricating the moving parts of a tire shredder according to the our instructions can prevent premature wear and keep the machine running smoothly.
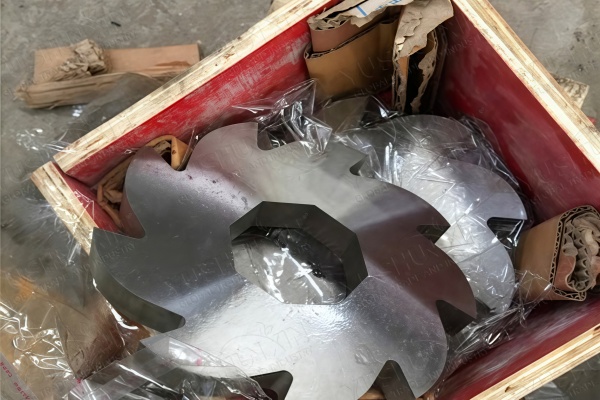
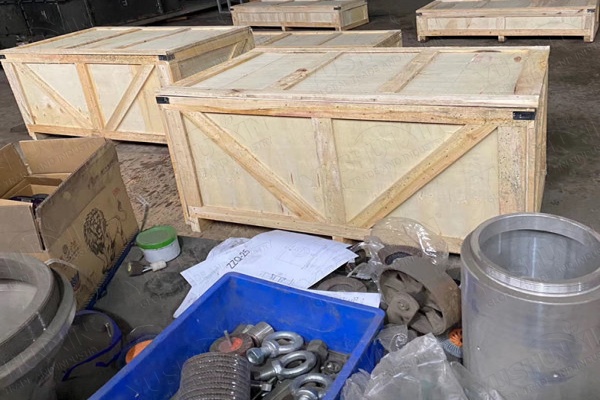
We will include spare parts with the machine during shipping. This includes items like the seals and gaskets in the pyrolysis furnace, which are important for preventing gas leaks. The same goes for shredders, where the blades wear out and need to be replaced. We’ll make sure you have these parts when you need them. If you don’t have the parts you need later, let us know and we will pack and ship them for you within 24 hours.
III. Value – Added Product Diversification
Profitability in Recycled Tyre Byproducts
To make your business more profitable, look at other products you can make from recycled tyres. Make high-value items like rubber mats for factories and homes. Also, research new markets for recycled tyres. The demand for sustainable building materials means there is a chance to make niche products like roofing and insulation using recycled tyre rubber. By trying new things, you can make your business more competitive and make more money.
Quality Control
Ensure high – quality production of your recycled tire products. Implement strict quality control measures to produce consistent and reliable products. For example, if you’re making rubber crumbs for use in playgrounds, make sure they meet the required safety and quality standards. This will enhance your reputation and allow you to command higher prices in the market.
How Profitable is Tire Recycling Business?
What are the Final Products
The profitability of tire recycling is significantly influenced by the prices of pyrolysis oil and carbon black, which are two main products obtained from the process. Pyrolysis oil, as one of the key products in the recycling process, has a wide range of applications. Carbon black, on the other hand, is also an important material that cannot be ignored, serving as a crucial ingredient in the manufacturing of rubber products, inks, and pigments.
Prices of carbon black and pyrolysis oil
The price of pyrolysis oil typically ranges from $0.30 to $0.60 per liter, depending on market conditions and its quality. Changes in market supply and demand, crude oil price trends, as well as the purity and composition of pyrolysis oil can all cause price fluctuations.
In contrast, carbon black, as a valuable material, plays a key role in multiple industrial fields. Its market price ranges from $0.80 to $1.50 per kg. The quality grade of carbon black, differences in application requirements, and the competitive landscape of the global market all affect its selling price.
Profit Potential of a tire recycling plant
A well-equipped and efficiently operated waste tyre recycling plant can produce a considerable amount of these products. For example, a medium-sized plant might generate several thousand liters of pyrolysis oil and several tons of carbon black per month. When the revenues from these products are combined and after deducting operating costs, there is a potential for a healthy profit margin, making tire recycling a viable and potentially lucrative business venture.
Contact Us