On 24 October, we received an inquiry from a German client about waste tyre pyrolysis recycling plant in Germany. The client wants to know more about YSX waste tyre pyrolysis machines. Because Germany offers financial subsidies and incentives for recycling, and Germany produces millions of tyres a year, so they have a big waste tire management problem. Pyrolysis, a form of WtE, could be the answer. The client wants to know if pyrolysis technology can be used for tire recovery and how. The following is what we talked about with the German client.
How to build a tire pyrolysis facility in Germany in 3 steps?
The German tire market is huge and is expected to grow at a CAGR of 3.80% during 2024-2032. With sufficient supply of scrap tires as raw materials, our German customers are interested in setting up a tire pyrolysis plant. They asked about the details of setting up a plant to start the business as they are considering using it for scrap tire management and recycling projects. To answer their questions about scrap tire pyrolysis, let’s start with three steps.
preparations for the tire pyrolysis plant
Step 2 to build a tire pyrolysis plant in Germany
Step 3 to build a tyre pyrolysis facility in Germany
What are the products of tire pyrolysis?
How to Choose Pyrolysis Furnaces for Tire Pyrolysis Plant?
Then we keep discussing with the German client. The client wants to set up a pyrolysis plant to recycle tyres and other rubber waste. They inquire which pyrolysis furnaces are best for their recycling plant.
Actually when choosing a tire pyrolysis furnace, it’s essential to consider different operating modes such as Batch, Semi – continuous, and Fully continuous.
Furnace Performance and Efficiency
Pyrolysis Plant Installation
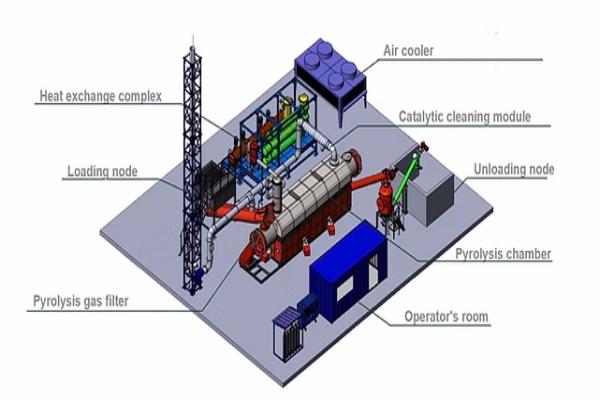
Tyre pyrolysis machine
Parameters of YUSHUNXIN pyrolysis furnace
Item | Waste pyrolysis unit | ||
Equipment type | Batch | Semi-continuous | Fully continuous |
Raw materials | Rubber tyres, plastics, oil sludge, coal tar, aluminium plastics, etc. | ||
Structure form | Horizontal rotation | ||
24-hour capacity | 100 kg-20 tonnes | 10-20 tonnes | 15-50 tonnes |
Oil yield From | 30-70 per cent | ||
Operating pressure | Normal | ||
Pyrolysis reactor material | Q245/345R, boiler plate, stainless steel | ||
Thickness of pyrolysis reactor | 14, 16, 18, 20 mm | ||
Speed of pyrolysis reactor | 0.4 rpm | ||
Total power | ≤ 30KW | ||
Cooling mode | Circulating water cooling | ||
Condenser cooling area | 100 square metres | ||
Type of transmission | Internal gearing | ||
Weight | Depending on size |
Average oil yield in the waste tyre pyrolysis plant featuring with auto-feeder
How much profit can you make from tire pyrolysis recycling?
The client wants to invest in a tyre-recycling plant now. Therefore, they asked about the profit from tyre pyrolysis recycling. “We wanted to know how much money this recycling production line could make.” This is also a question that most customers are very concerned about. Actually this depends on many things.
Scale of Your Pyrolysis Plant
Pyrolysis Product Prices and Market Demand
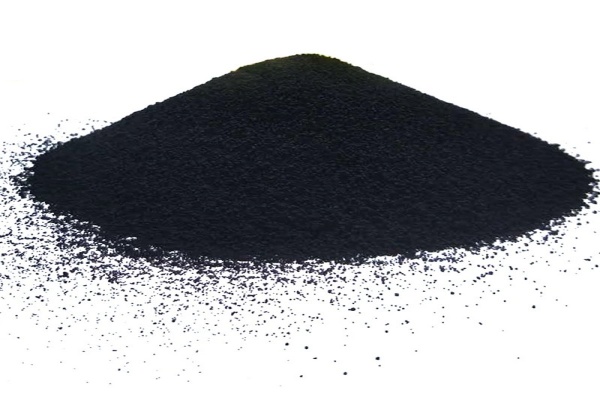
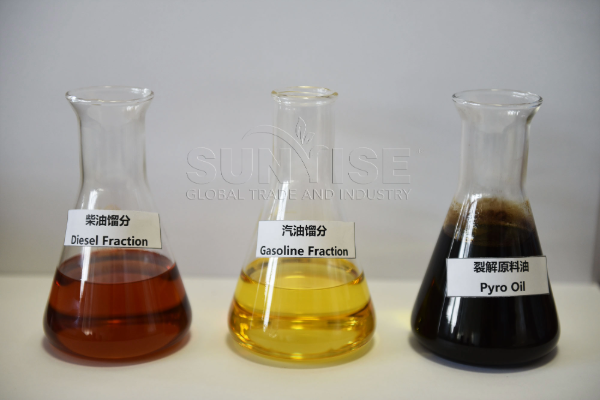
Is there any customized scrap tire pyrolysis solution reference?
oLet’s differentiate based on processing capacity. The following we’ll provide you with German waste tire pyrolysis recycling production line of different scales for reference. Customers can make adjustments as needed:
Small tire pyrolysis recycling production line proposal (suitable for start-ups or experimental production)
The daily processing volume of waste tires is about 1-2 tons, mainly producing rubber particles, some steel wires, and pyrolysis oil.
Before pyrolysis
Pyrolysis machine(optional)
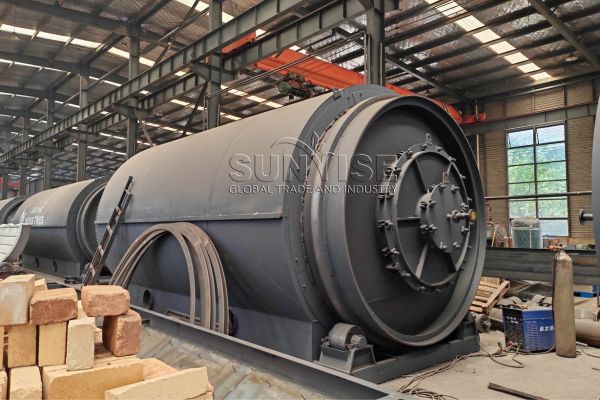
Other aspects of the pyrolysis solution
Medium tire recycling production line solution (regional market)
The daily processing volume of waste tires is 5-10 tons, and high-quality rubber particles and high-quality carbon black are produced for tire retreading or high-end rubber production, and recycled steel wire is sold. The pyrolysis oil meets the industrial fuel standard and is partly used for self-use and partly sold.
Before pyrolysis
Pyrolysis machine(optional)
Continuous tire pyrolysis furnace: It produces 1-2 tons of pyrolysis oil and 0.8-1.2 tons of carbon black per day, uses natural gas or biomass particles as fuel, has a thermal efficiency of more than 70%, and is equipped with waste heat recovery for drying and other links.
Other aspects of the pyrolysis solution
Large-scale tire recycling production line plan (industrial cluster)
Daily processing of 20 tons or more of waste tires, large-scale production of high-quality rubber product raw materials, carbon black, and steel wire, and pyrolysis oil for park energy or external sales.
Equipment layout before pyrolysis
Pyrolysis and deep utilization cluster
High-efficiency large-scale pyrolysis furnace group: multiple continuous pyrolysis furnaces in parallel, daily output of 5-8 tons of pyrolysis oil and 3-5 tons of carbon black, advanced heat recovery and automatic control to ensure stable operation.
Carbon black modification and granulation production line: Deep modification and granulation of carbon black to meet the needs of tires and high-end rubber, with strong product competitiveness; pyrolysis oil refining device purification reaches the high-quality standard of fuel oil.
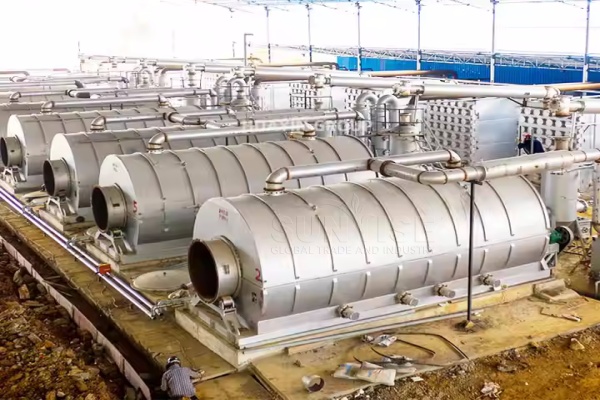
Other aspects of the pyrolysis solution
Why Choose YSX as your Pyrolysis Furnace Supplier?
What Qualifications Do We Have?
At SUNRISE, CE and ISO 9001 certifications are just part of our offerings in this regard. We’ve got a whole slew of other certifications up our sleeve to meet diverse compliance and quality benchmarks as well.
Customer feedback pictures of pyrolysis plant
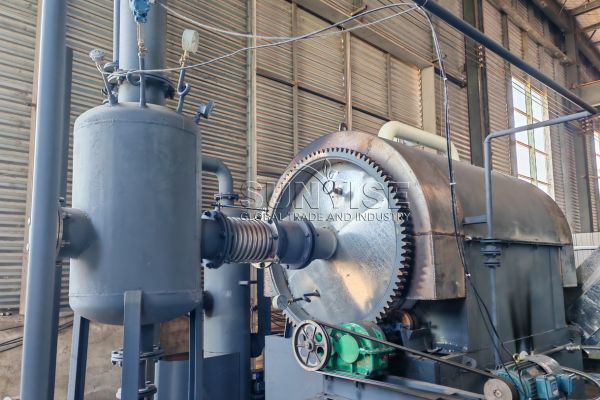
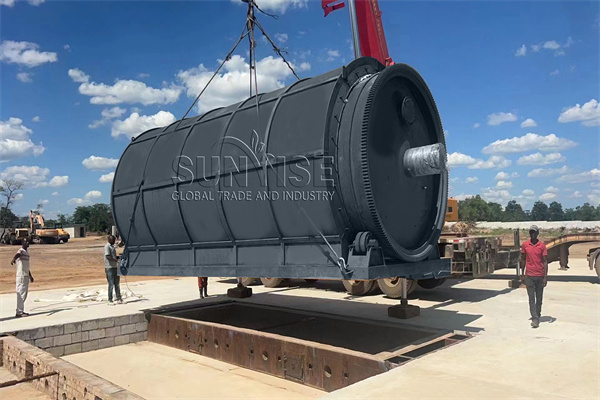
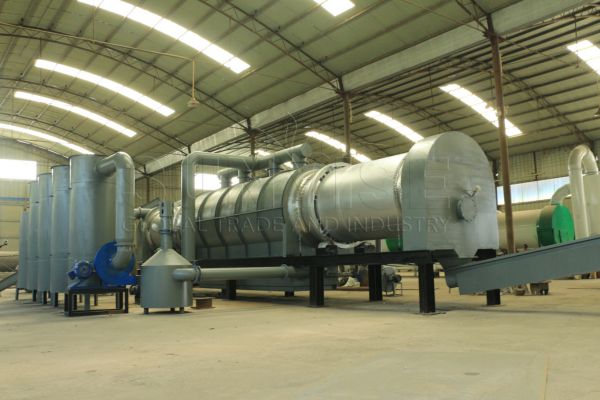
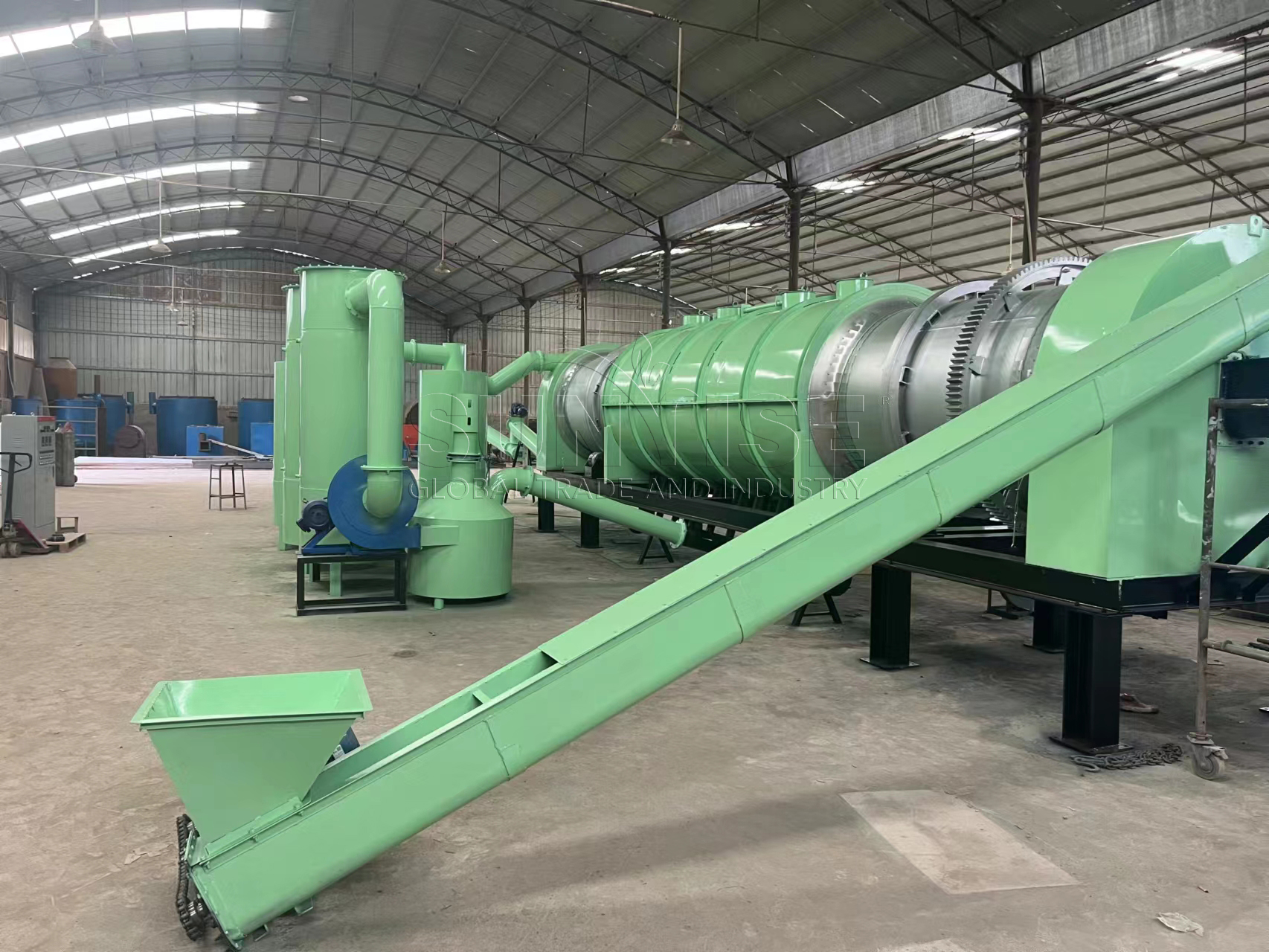
Finally, our German customers want to know how pyrolysis works in specific production case studies. This can help them decide if this technology is right for them. Let’s take a look at some great examples. Click here to know more.
YSX team can provide you not only the tire reycling solutions, but also e-waste disposal plan like batteries recycling solutions, circuit board recycling solutions, and solar panel reycling solutions. Feel free to contact us if you wanna start recycling business.
Contact Us